Introduction:
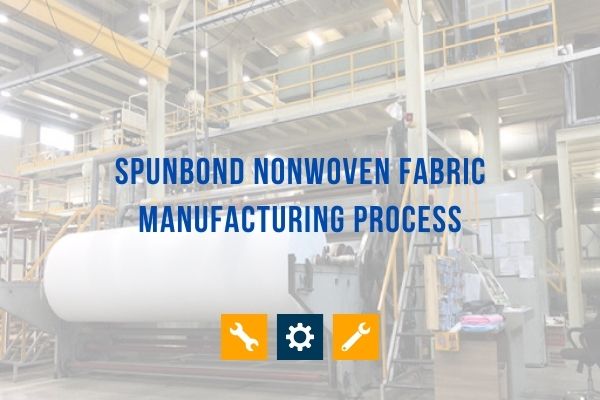
Meltblown nonwoven fabric has gained widespread recognition for its versatility and exceptional filtering capabilities. As the demand for this fabric continues to rise, manufacturers are constantly seeking innovative solutions to enhance production efficiency. In this blog, we will explore the revolutionary PP meltblown nonwoven fabric making machine, an advanced technology that is transforming the manufacturing process. We will delve into the intricacies of this machine while highlighting its relevance in the industry.
Keywords: Meltblown nonwoven fabric making machine, manufacturing process, PP meltblown, production efficiency, advanced technology
The Importance of Meltblown Nonwoven Fabric:
Meltblown nonwoven fabric stands out as a crucial material in various industries, such as pharmaceuticals, filtration, medical devices, and personal protective equipment. Its intricate fiber structure allows for exceptional filtration performance while maintaining breathability. The recent surge in demand for face masks and other protective gear amidst the COVID-19 pandemic has significantly emphasized the importance of meltblown nonwoven fabric.
The Need for Advanced Manufacturing Equipment:
Efficient production of meltblown nonwoven fabric requires advanced machinery capable of converting molten polypropylene (PP) into ultra-fine fibers and subsequently forming them into a web structure. Traditionally, this process involved complex and time-consuming procedures, resulting in limited production capacities. However, the advent of the PP meltblown nonwoven fabric making machine has revolutionized the manufacturing process, allowing for higher production rates and superior fabric quality.
Understanding the PP Meltblown Nonwoven Fabric Making Machine:
The PP meltblown nonwoven fabric making machine is a state-of-the-art equipment specifically designed to automate the production process, eliminating manual intervention and increasing overall efficiency. This machine encompasses various stages, including extrusion, filtration, meltblown, cooling, and winding. Each stage plays a vital role in achieving the desired fabric properties.
1. Extrusion:
The process begins with the extrusion section, where the PP granules are melted and transformed into a viscous liquid state. This molten material is then passed through a spinneret containing micro-sized holes, forming a continuous stream of fine fibers.
2. Filtration:
To ensure the uniformity and quality of the fibers, the extruded material undergoes a thorough filtration process. This step removes any impurities or solid particles present, guaranteeing a highly pure and consistent melt.
3. Meltblown:
The filtered melt is then directed to the meltblown chamber, where it encounters high-velocity hot air. This interaction causes the fibers to stretch and thin down to their desired diameter, resulting in the formation of a microfiber web.
4. Cooling:
The newly formed nonwoven fabric undergoes rapid cooling to solidify the fibers, allowing them to retain their shape and improve their structural integrity. The cooling process also enhances the fabric's overall quality and dimensional stability.
5. Winding:
Finally, the meltblown nonwoven fabric is wound into rolls of various widths, ready for subsequent processing or direct usage in manufacturing applications.
Benefits of the PP Meltblown Nonwoven Fabric Making Machine:
The advanced features and automated functionality of the PP meltblown nonwoven fabric making machine offer numerous advantages for manufacturers:
1. Increased Production Efficiency:
By eliminating manual intervention and streamlining the manufacturing process, the machine significantly increases production rates. This allows manufacturers to meet the ever-growing demand for meltblown nonwoven fabric in a timely manner.
2. Consistent Fabric Quality:
The tightly controlled parameters of the machine ensure that the produced fabric maintains its desired properties, such as filtration efficiency, basis weight, and fiber size. This consistency is crucial for industries reliant on high-quality meltblown nonwoven fabric.
3. Cost Reduction:
Automated operations theoretically reduce labor costs, as minimal human involvement is required. Additionally, the machine's optimization of material usage results in reduced waste, leading to potential savings in raw material expenses.
4. Flexibility and Customizability:
The machine's design allows for easy adjustments, facilitating the production of meltblown nonwoven fabric with varying characteristics. Manufacturers can adapt their production processes to meet specific industry requirements without any major modifications to the machine.
Conclusion:
The PP meltblown nonwoven fabric making machine has revolutionized the manufacturing process of this highly sought-after fabric. Its advanced technology and automated functionalities have increased production efficiency, maintained consistent fabric quality, reduced costs, and enhanced flexibility. As the demand for meltblown nonwoven fabric continues to grow, this machine plays a pivotal role in meeting market requirements while ensuring the highest standards of performance and reliability.